Palmet Energy Group succesfully completed the acquisition of IZGAZ Izmit City Gas Distribution and Baymina Enerji A.Ş previously owned by one of the most important energy companies in the world ”the French ENGIE group”, as of March 8, 2021.
With this acquisiton ,Palmet Energy Group is growing in electricity production business. Adding Baymina Natural Gas Cycle Power Plant in Ankara to the natural gas cycle power plants in Lüleburgaz and Aydın, Palmet Energy reached a total installed power generation capacity of 892 Mwe’s.
I was the acting project director in the renovation, re-commisioning and development works at the Baymina Natural Gas Fired Power Plant which has not been in operation since 2019 (was mothballed by the Engie Group). Our operations team successfuly re-commisioned the plant and the plant was synronised to the Turkish power grid on the 1st of June 2021 with its full power generation capacity of 770 Mwe’s.
The plant efficiency of Baymina operating in free market conditions (ie. without a power purchase agreeement / guarantt) has been announced %57.6 by Palmet Energy group. Please refer to Palmet Group web sites for further information.
The main plant equipment are ;
2 nos. of GE 9FA Gas Turbines (each rated power output 235 Mwe)
2 nos. of GE 309 MVA Hydrogen cooled generator (15.75 kV)
1 no. of GE ALSTOM DKY224-4N4/B (rated power output 320 Mwe)
1 no of ALSTOM 380 MVA generator (18.5 kV)
2nos. of COCKERILL MECHANICAL INDUSTRIES Heat Recovery Steam Generator (with supplementary Duct Burner firing)
2 nos. of water cooled cooling towers
Water Pre-treatment plant (WPTP)
Demineralized Water Production plant
The re-commisioning activities started in March 2021. All 3 generation sets (2 9FA turbines and the steam turbine) were boroscope inspected and fully cold commisioning according to vendor’s requirements. The 2 HRSG’s were visualy inspected and critical components were NDT tested. The WPTP (Water Pre Treatment Plant) was fully cleaned, supplied with new chemicals. All aux. Systems (pumps, valves, dcs systems etc) were re-commisioned. The Demineralized Water Production Plant was re-commisioned. All plant high voltage and middle voltage systems were tested and re commisioned (154 kV and 6.6 kV systems, transformers, switchyards, switchgears etc), all plant auxilary systems were fully maintained and re-commisioned.
Some photos taken during the re-commisioning activities and their brief descriptions are as seen below.

The General Electric GE 9FA type heavy duty gas turbine. Single shaft 14 stage compressor, 3 stage turbine, F-class 50 Hz 3000 rpm, Dry Low Nox (DLN) combustion system. Power output is 235 MWe at site conditions.

The DLN combustion cans , total of 18 cans. Each can supplied with D5, PM1 and PM4 fuel nozzles to support various combustion modes ; diffusion mode (D5 only) , sub-piloted premix (D5+PM1) , piloted premix (D5+PM1+PM4) and premix modes (PM1+PM4)
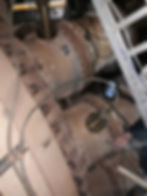
Boroscope inspection of combustion cans (A more detailed boroscope inspection blog entry will be available in the future)
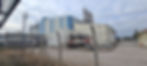
Power Plant PRS-A station (operated by Başkent Gaz). Natural gas from the Turish gas grid is supplied at around ~70 barg, which is filtered, regulated down to ~40barg and mesaured prior to entering the Baymina power plant.

Owners gas station, the PRS located inside Baymina with futher regulates the gas pressure down to ~30 barg (ie. the gas turbine operating pressure) and measures gas flow for cross checking with gas supplier. Natural is heated upto ~170oC prior to entering the turbine.
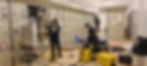
Maintenance and re-commisiong works on the 6.6kV switch gear systems

154 kV Switcyard maintenance works.

Maintenance works on 3 main step-up transformers. Step-up Transformers of Gas Turbine 1 and 2 are 15,75/154kV and for the steam Turbine 18,5/154kV

We had many high level visitors during the re-commisioning activities of the power plant. In the back ground the HRSG-1 (Heat Recovery Steam generator of gas turbine-1) is visible

A general view of the power plant where we can see the 2 nos. of water cooled cooling towers, mechanical workshop building and our storm water pond.
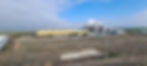
A general view of Baymina Power plant, where we can see cooling towers, the 2 nos. of HRSGs, the machine hall, Baskent Gas PRS-A station.

The main entrance gate to the power plant. This photo was taken on 23rd of April which is the "National Sovereignty Day" of Turkey.

Visit of the KKB's management team during our re-start project. Palmet was the main contractor for KKB's Uptime Institure Tier IV certified datacenter in Ankara. The LP (low pressure) section of the steam turbine is visible in the back ground.

Inside the machine hall, the middle section of the machine hall is the steam turbine block, which is sitting above the concrete foundation on top of the concrete pillers. The green box seen below the steam turbine is the condanser block.

Here is a lovely shot inside the steam turbine condanser during the re-commisioning of the power plant. All the tube bundles were examined inspected and cleaned prior to the cold commisioning activities of the steam turbine. This volume is under constant vacuum during plant operation.
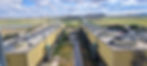
The cooling towers, each equipped with 8 no. of fans (each fan diameter ~8meters). There are a total of 8 riser blocks (the green pipes seen in the photo).

Cooling tower basin. The two cooling towers are connected to each other, so it is a single pool actually. Each cooling tower is approximately 100 meters long x 20 meters wide. All concrete sub-structures of the cooling tower basin are coated with protective coating to reduce wear and tear due to the chemicals used during water treatment processes.

Cooling tower basin, by-pass pipes.

A very cool photo of the cooling tower taken in the dark during plant operation. The evaporation loses of the power plant during summer times can be as high as 1000 m3 of water per hour and during winter times around 400~500 m3/hr depending on ambient conditions and plant power load.
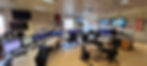
The operation and control room. Plant DCS system is monitored and managed from this room.